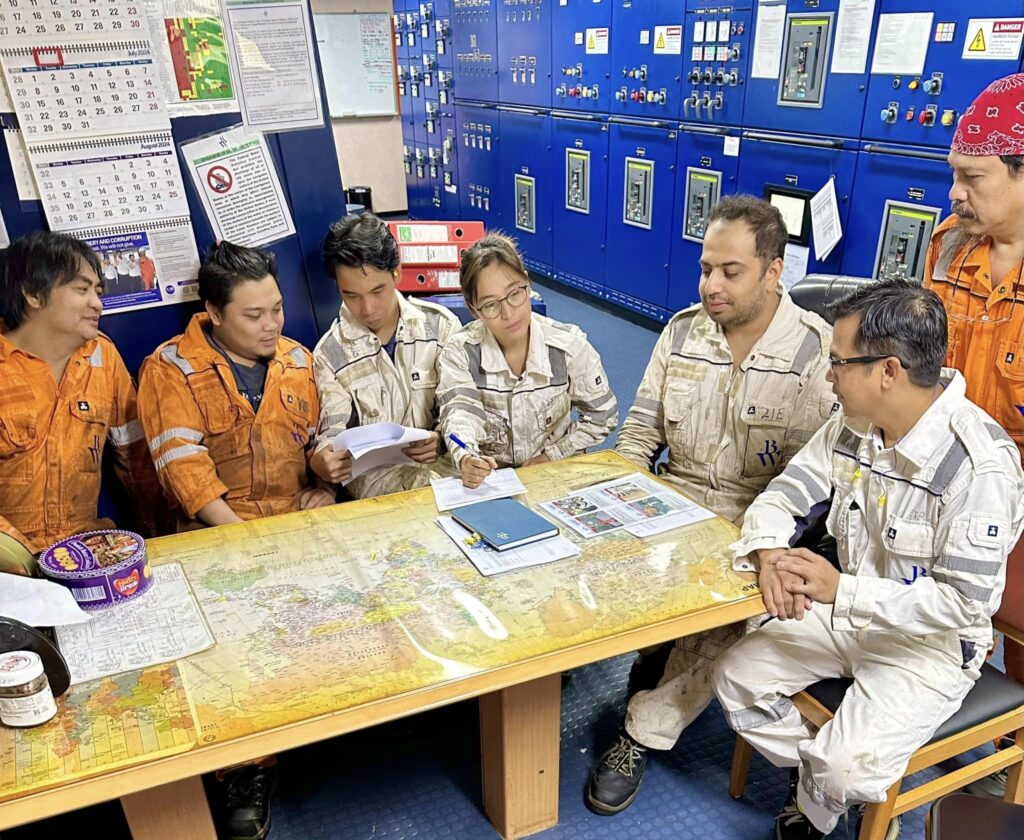
BW LPG has been delivering cleaner-burning energy to world markets for over 50 years. Our reputation as a safe, reliable, and sustainable business partner is built on many strengths, one of which is flawless operations. A key aspect of flawless operations is attention to detail, including the management of spare parts onboard. Having the right equipment and parts onboard can make a significant difference in minimizing downtime, reducing costs, and enhancing overall operational efficiency and business success.
Spare Parts Mastery Campaign
BW LPG launched a campaign to raise awareness among our crew on the importance of managing spare parts well onboard and to provide them with the best practices, tools, and process awareness to succeed.
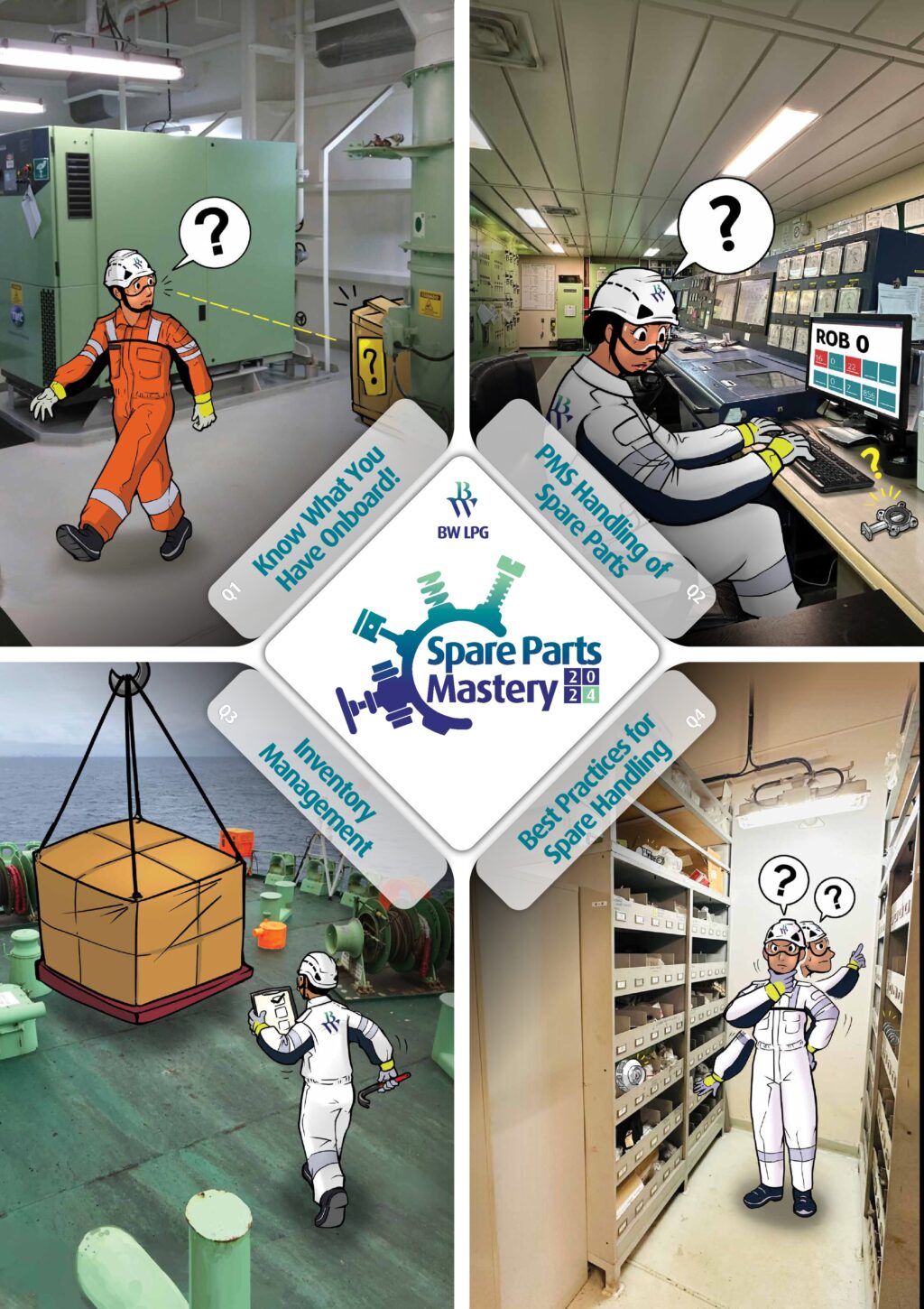
Quarter 1: Know What You Have Onboard
The campaign has four themes, each lasting a quarter. It kicked off in the first quarter with a simple guidance: know what you have onboard. Crew members were reminded that small, sustained efforts go a long way in managing equipment. Boxes should be labeled and referenced, all parts should be registered in an inventory management system, items should be kept in designated places, and all materials should always be safely stowed. Crew should also be curious enough to open unmarked boxes and check their content.
Quarter 2: PMS Handling of Spare Parts
In the second quarter, the focus shifted to the proper use of the company’s Planned Maintenance System (PMS). The quarter was based on vessel input and participation, brainstorming on what is working well, what could be improved, and the sharing of best practices amongst our vessels.
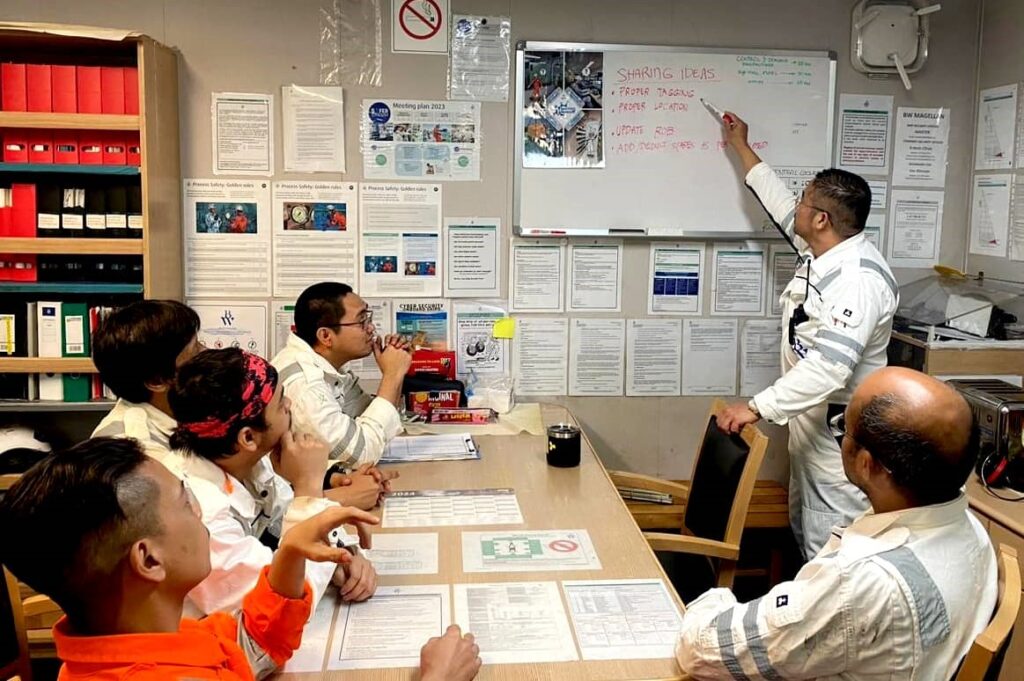
Quarter 3: Inventory Management
As we head into the third quarter, workflows related to ordering and receiving spare parts will be discussed. Best practices include checking deliveries against order lists; reporting incorrect, missing, or damaged items; storing items promptly and in designated locations; and acknowledging goods received in the procurement system promptly. New initiatives for making inventory more efficient and a warehouse strategy will also be part of this quarter’s campaign.
Quarter 4: Best Practices for Spare Parts Handling
In the final quarter of the campaign, we will look at housekeeping habits to keep the vessel’s storeroom tidy. Boxes should not be stored on the floor where possible, parts should be stored in accordance with what is described in the PMS. The most efficient ways to handle and store spare parts will also be touched upon. While maintaining neat and tidy spare parts management can test anyone’s discipline, it is critical to flawless operations.
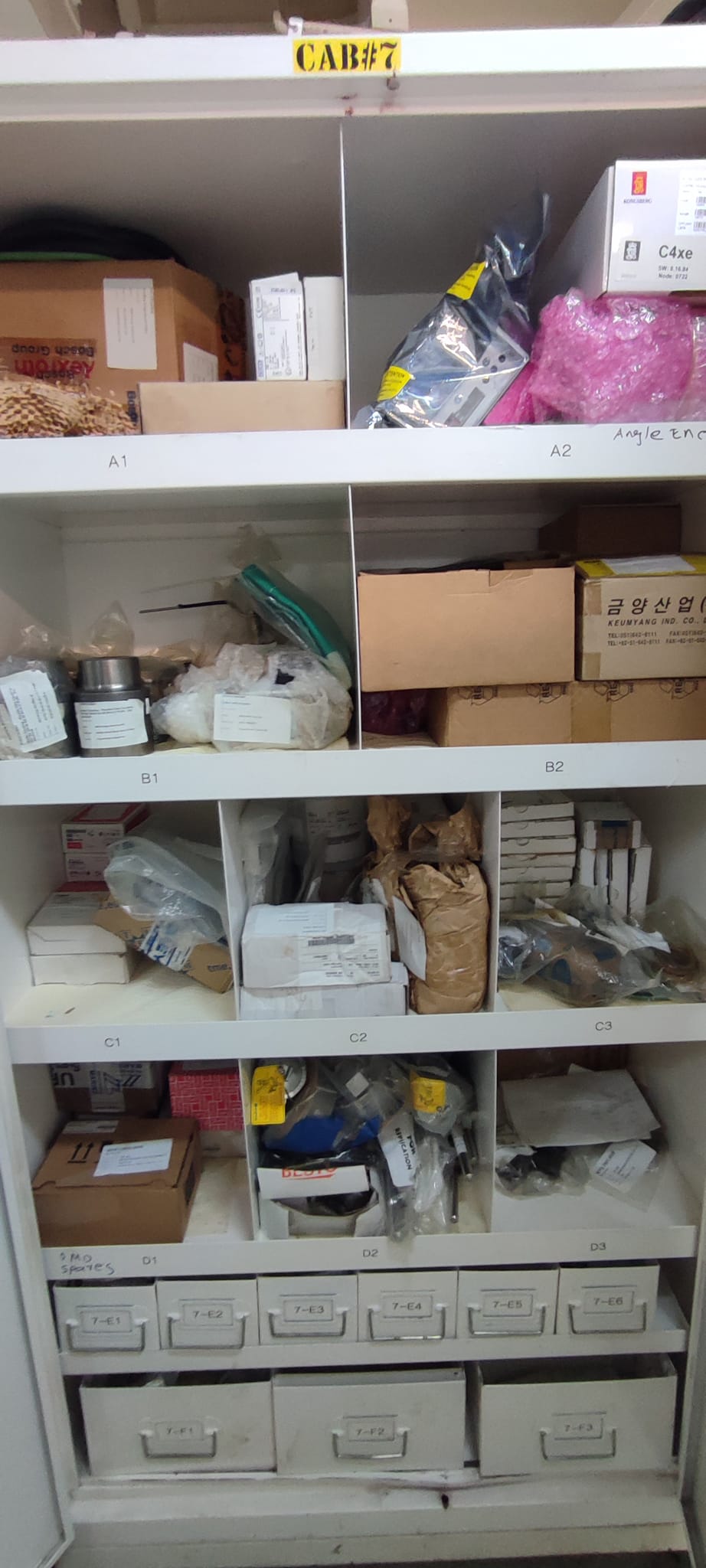
Benefits of Good Inventory Management
No matter how well-maintained a vessel is, unplanned downtime is inevitable. Prioritizing the availability of spare parts for critical machinery ensures quick responses to emergency repairs. By keeping essential spares on hand, businesses can minimize stoppages and downtime losses, especially when operations are time sensitive. Effective spare parts management also helps minimize operational expenses and overstocking of parts, some of which may incur storage costs.
What does success look like at the end of the campaign? We hope to see a change in the way our crew approaches spare parts management, translating to reduced logistics costs and expected operating expenses. Looking at photos submitted by vessels, the campaign is on the right track. Fleet Manager Martin Burton says, “The goal of this year-long campaign is to change our attitude and approach towards the management of spare parts. By focusing on enhancing the efficiency and effectiveness of spare parts management daily, we can achieve significant long-term benefits.”