Material Topic for BW LPG
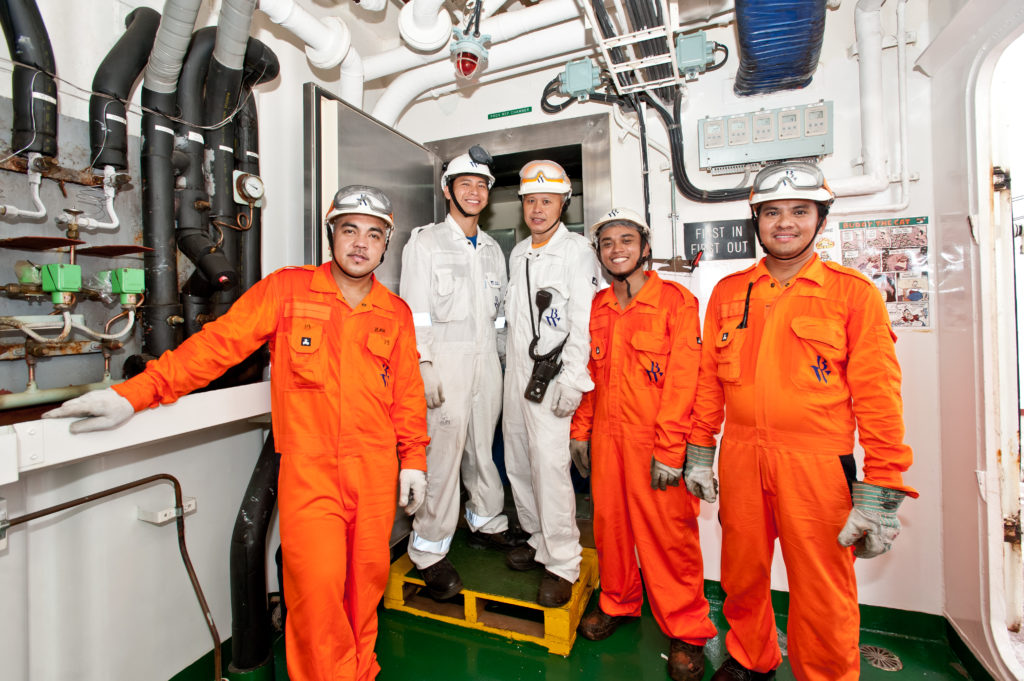
Risk, Commitment, Value
Risk
Reliance on third party contractors and services providers can increase operational risks because of trickle-down impacts from disruptions in the supply chain.
Commitment
Incorporate ESG considerations as a strategic criteria throughout various stages of the supplier life cycle. We seek to achieve comprehensive visibility into supplier performance by fostering collaboration and engagement, promoting co-development and innovation with suppliers towards a sustainable supply chain.
Value
Mitigating sustainability risks within our supply chain not only reinforces stakeholders’ confidence in our brand but also positions us for compliance with future regulations on supply chain due diligence.
Our Approach
Responsible Procurement
We are committed to the safe and sustainable operations of our business, and one way we do so is by upholding strict practices in procurement, as outlined in our BW LPG Procurement Policy. We work with our suppliers to raise their awareness of sustainable practices and engage them in conversations to help improve their own operations. By enhancing our supply chain, we mitigate risks and uphold ethical sourcing standards. As a condition of business, suppliers must commit to our Supplier Code of Conduct, and Terms and Conditions.
Contractor Management
Our relationships with contractors are fundamental to our business success as we regularly engage their services for maintenance works and occasional dry dockings. Together with our technical superintendents, we manage these strategic relationships between third parties, contractors and shipyards.
By influencing our suppliers to improve sustainability practices, together we can play our part in supporting responsible procurement and contractor management.
100% of new suppliers engaged in 2022 made a signed commitment to BW LPG’s procurement policy | Region | Vendors | Spending |
1 Europe | 140 | 48% | |
2 Far East Asia | 57 | 19% | |
3 North America | 31 | 11% | |
4 Others | 66 | 22% | |
Total | 294 | 100% |
Supplier Selection
Tenderers compete in a transparent environment with clear selection processes based on objective criteria and equal opportunity. New suppliers are screened using internal criteria such as quality, delivery, reliability and price, and requirements for specific certifications, including Quality Management System (ISO 9001) and Environmental Management System (ISO 14001).
In addition, all suppliers need to meet our expectations on Environment, Social and Governance (“ESG”) standards, which are covered in our Supplier Code of Ethics and Business Conduct (“SCEBC”). Our SCEBC was also recently updated to mandate that our suppliers respect human rights as set out in the United Nations Universal Declaration of Human Rights and endorse the principles of the UN Global Compact and the OECD guidelines for multinational enterprises.
In 2021, we conducted a review of our procurement practices and identified key areas for improvement. A survey on ESG practices was done on our suppliers, and we categorised them according to their maturity and quality, such as having ISO certification and plastics reduction initiatives. This preliminary result serves as a foundation to enhance our ESG-procurement plan and foster sustainable change through communication with suppliers.
Human Rights and Decent Working Conditions
We want to promote enterprises’ respect for fundamental human rights and decent working conditions in connection with the production of goods and the provision of services. Information on how enterprises address adverse impacts on human rights and decent working conditions should be made publicly available.
SupplierPerformance Management and Evaluation
At BW LPG, internal checks and balances include an International Marine Purchasing Association (IMPA) standard selection questionnaire to assess the quality and compliance of suppliers. We evaluate the certifications and standards suppliers adhere to (ISO 19001, ISO 14001, Health and Safety, and Environmental Management systems, hazardous goods handling policy etc.). We also distribute a post-work performance review among crew and employees, to gather feedback on the performance and interactions with suppliers.
In 2022, we partnered with Sustainalytics Supply Chain Solutions to assess the ESG risks of our suppliers. We evaluated >200 active suppliers to review gaps in their current ESG policies and practices. 50 suppliers underwent a supplier performance audit where suggested improvements were communicated. Critical suppliers were audited through a third-party provider.
The Procurement team ensures that corrective actions are taken to rectify supplier non-conformance, and that they receive adequate training. The team also encourages suppliers to extend sustainable practices down their supply chain.
Vessels frequently host external contractors onboard for activities such as maintenance work, surveying, security, and pilotage. For all work performed, we have guidelines and procedures to ensure Zero Harm to our people and the external contractors we work with.
Supplier Audit
A third-party supply chain auditor assess suppliers’ Corporate Social Responsibility and quality assurance practices of key suppliers. The off-site audit includes verifying that documented policies align with our Supplier Code of Conduct, and that suppliers meet requirements from our vendor selection process.
Results from the audit are collated in our supply chain management system. Under-performing or non-compliant suppliers are reviewed and notified with a timeline set for improvements.
Initiatives
Reducing Plastics
In conjunction with our pledge to IMPA Save initiative, we:
- Stopped the purchase of single-use plastics on board and on shore where possible. This includes cups, cutlery, straws, plastic bags and single-use water bottles
- Provided reusable water bottles and installed water dispensers to all BW managed vessels
- Updated our supplier terms and conditions to include a request for suppliers to minimise plastic use
- Continued initiative to return pallet plastic shrink wrap to suppliers at specific ports. All plastic from BW LPG landed at ports are recorded and a report is provided on a quarterly basis
Reducing Plastics
We aim to enhance onboard inventory and procurement process. To reduce turnaround time, transportation costs and potential emissions footprint reduction. Objectives include:
- Visibility of spare parts
- Reduce supplier procurement and delivery lead-times
- Automated replenishment of stock levels in the warehouse
- Greater efficiency with less Purchase Orders
- Lower transport costs as we can transport more in bulk via Sea freight or standard airfreight instead of Express.
- Lower OPEX
Collaboration
BW LPG regularly collaborates with other affiliates within the BW Group to share knowledge and best practices on procurement, with the aim to streamline processes and policies, leverage on each other’s understanding of the market and make full use of available resources. One positive outcome has been the creation of a new Resource Planning system, a one-stop solution for ship management purchasing which further automates the purchasing function for our fleet. A Procurement Manifest has also been set up to ensure mutually beneficial contracts for both BW LPG and our vendors. We leverage on volume and shared resources across affiliates to optimise the conditions of the contract and manage risks.
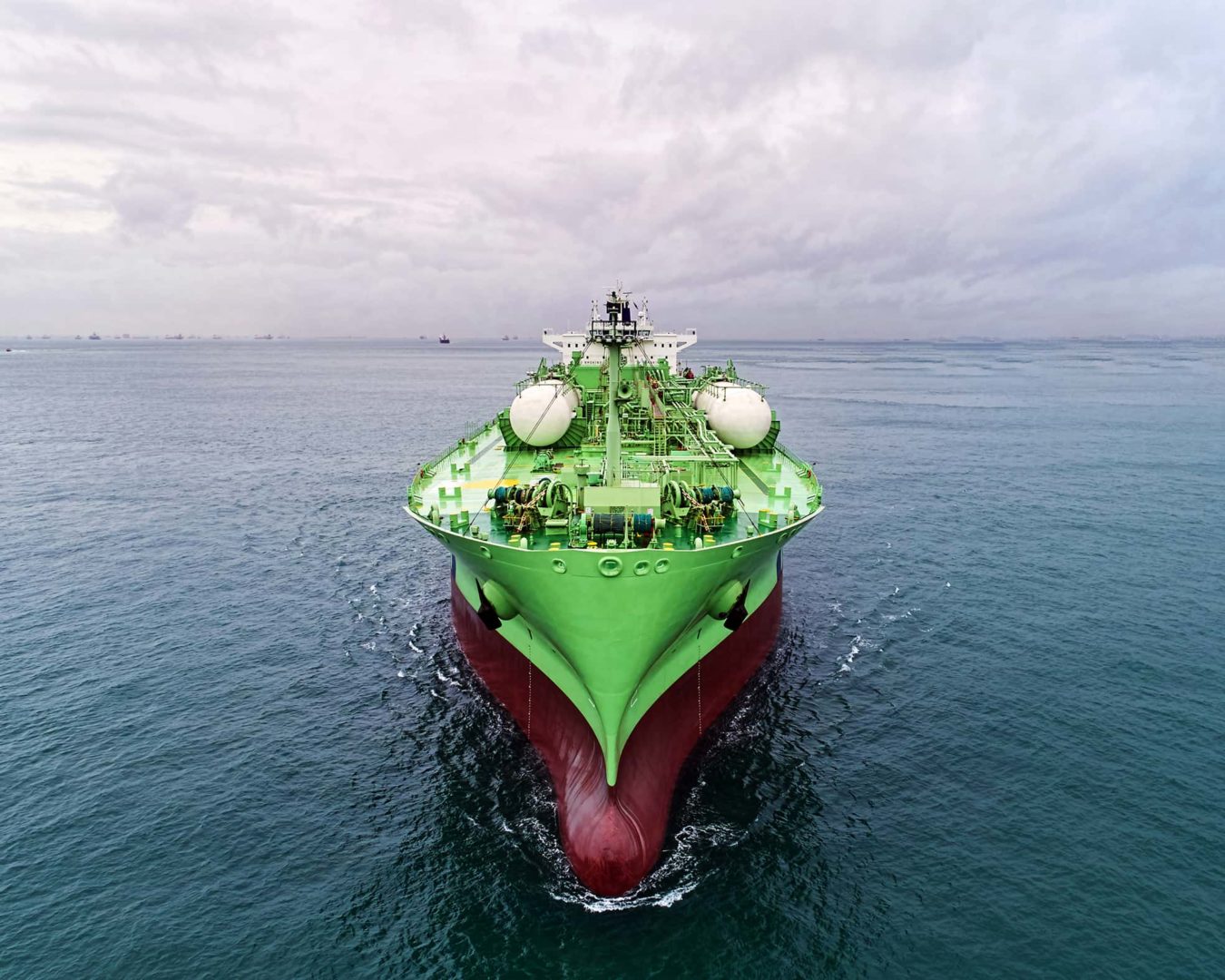
Sustainability Strategy and Governance
Guided by our Vision and Purpose, our sustainability strategy is based on three key pillars and are underpinned by our CARE values.
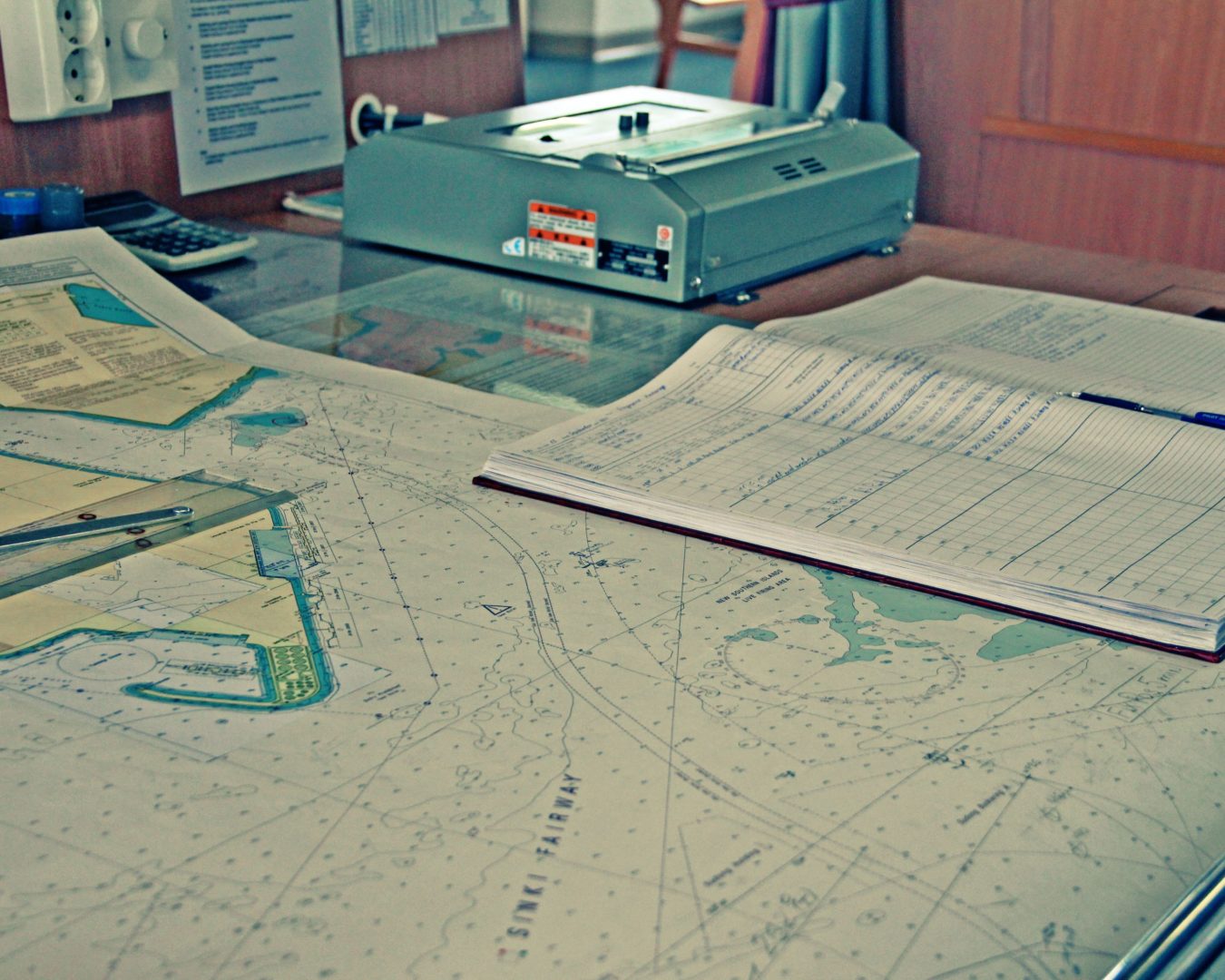
Targets and Performance
Committing ourselves to the transparent sharing of information on key ESG metrices so as to monitor our performance.
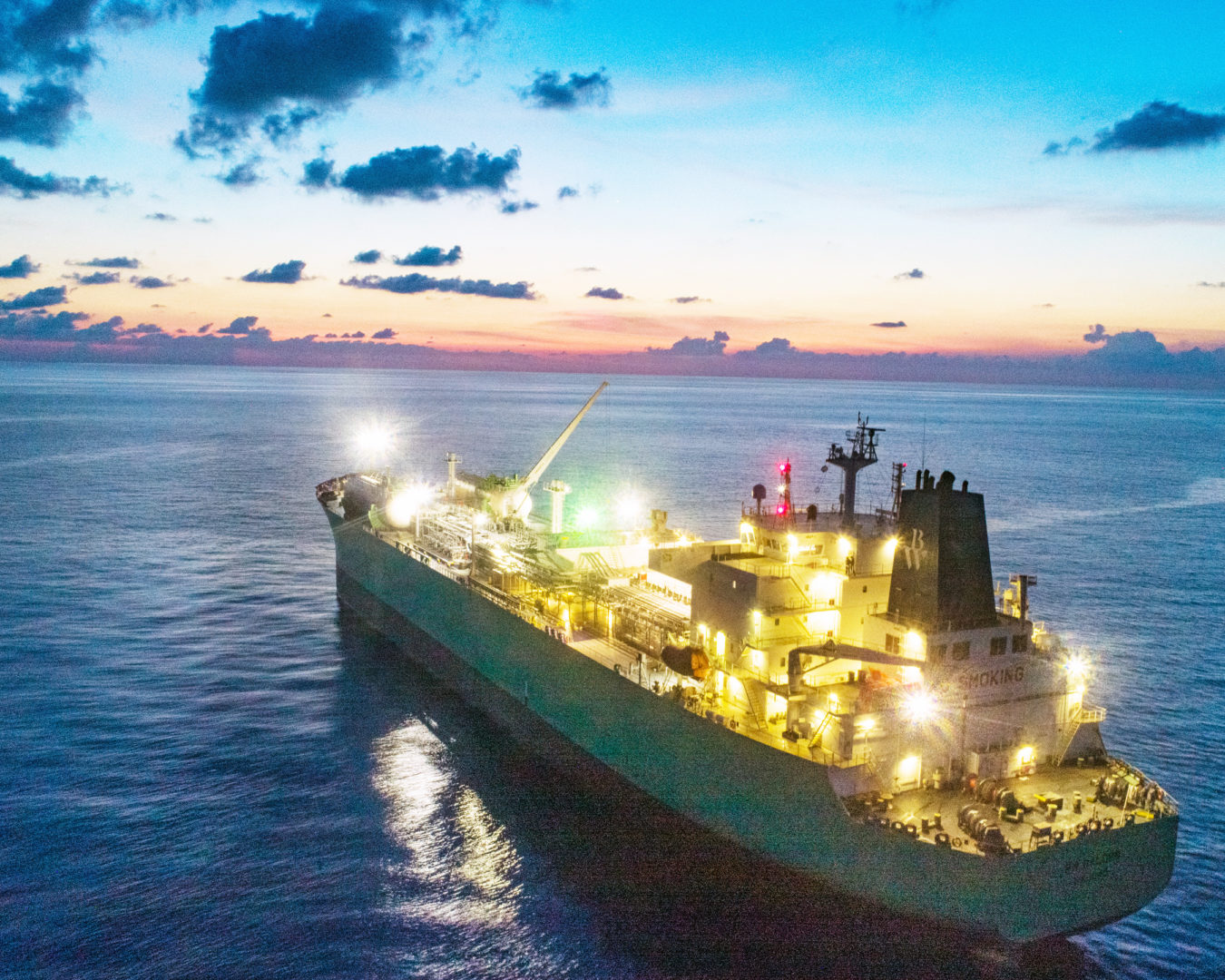
Policies and Guidelines
Communicating our standards for business conduct clearly and transparently through policies and guidelines.